High-performance Neodymium (NdFeB) magnets are made by balancing several things: remanence (Br), intrinsic coercivity (Hcj), and maximum energy product ((BH)max). These are important because we want to make magnets that have strong magnetic fields, don’t demagnetize, and use energy well. As people use more and more magnets in things like renewable energy, electric vehicles, and advanced electronics, it’s important to make sure we can get high Br and Hcj while using fewer resources. That’s where the grain boundary diffusion (GBD) process comes in. It lets us make better magnets while using less of the rare and expensive heavy rare earth elements (HREEs) like Dysprosium (Dy) and Terbium (Tb).
Challenges in Enhancing Neodymium Magnet Performance
Neodymium magnets are mostly made of Nd2Fe14B, which has super high saturation magnetization and excellent magnetocrystalline anisotropy. These properties are what make it such a great material for high-performance magnets. That’s why we use it when we want to make magnets with super high magnetic fields and that don’t demagnetize easily when they’re around other magnetic fields. One thing we’ve always struggled with is how to make the coercivity better without hurting the remanence.
The intrinsic coercivity of NdFeB magnets is mostly determined by the microstructure of the magnet. This includes things like grain size, the phase at the grain boundaries, and how the Nd-rich phases are dispersed. We usually add Dy and Tb to the magnet to increase the coercivity because they have a higher anisotropy field. The problem is that when you add them, you reduce the remanence. Also, Dy and Tb are expensive and hard to get. So, the trick has always been to increase the coercivity without hurting the remanence.
The targeted addition of HREEs using GBD technology can increase the coercivity of a magnet by 5 to 10 times or more, while reducing the amount of Dy or Tb needed by as much as 90%. By only adding the Dy or Tb to the surface of the magnet, the remanence, or the ability to hold a magnetic charge, remains unchanged. This is an important distinction because remanence is what gives a magnet its strength.
Grain Boundary Diffusion: Revolutionizing Coercivity Enhancement
The targeted addition of HREEs using GBD technology can increase the coercivity of a magnet by 5 to 10 times or more, while reducing the amount of Dy or Tb needed by as much as 90%. By only adding the Dy or Tb to the surface of the magnet, the remanence, or the ability to hold a magnetic charge, remains unchanged. This is an important distinction because remanence is what gives a magnet its strength.
Key Features of Grain Boundary Diffusion:
- Targeted Use of HREEs: Unlike traditional methods, where Dy and Tb are distributed throughout the entire magnet, GBD delivers HREEs specifically to grain boundaries. This ensures that only the critical regions requiring enhanced resistance to demagnetization receive these elements, resulting in a significant reduction (up to 70-100%) in the amount of HREEs required.
- Core-Shell Microstructure: During the GBD process, HREEs diffuse into the grain boundary regions, creating a core-shell structure where the outer layers of the magnetic grains are rich in Dy or Tb, while the inner core remains primarily Nd-rich. This boosts coercivity without diluting the magnetic strength of the main phase.
- Maintaining High Br: Because the HREEs are concentrated in the grain boundaries rather than the bulk of the magnet, GBD enables magnets to retain their high remanence (Br), a key advantage over traditional methods where HREEs uniformly dispersed throughout the magnet would reduce Br.
- Increased Coercivity: By reinforcing the grain boundaries with Dy or Tb, GBD strengthens the magnet’s ability to resist demagnetization, especially at high temperatures and in the presence of opposing magnetic fields. This is particularly critical for applications such as electric vehicle motors and wind turbines, where magnets are exposed to harsh operating conditions.
- Cost Efficiency: Given the high cost of HREEs, reducing their use without compromising performance is a significant advantage. GBD not only cuts down on the amount of Dy and Tb required but also stabilizes supply chains by conserving these valuable resources.
GBD vs. Traditional Technology
In traditional NdFeB magnet production, HREEs are introduced during the alloying process, leading to their even distribution throughout the magnet. While this enhances coercivity, it also results in the magnetic dilution effect, where the addition of Dy or Tb reduces remanence. Moreover, this method is resource-intensive, requiring large quantities of HREEs, which significantly drive up production costs.
In contrast, GBD localizes the introduction of HREEs, effectively enhancing coercivity where it is needed most—at the grain boundaries. This targeted diffusion technique maintains high remanence, reduces material costs, and allows for the development of new magnet grades with enhanced performance, previously unattainable with conventional methods.
Applications and Benefits of GBD Magnets
Grain boundary diffusion has opened up new possibilities for magnet applications, especially in industries that demand high-performance, high-coercivity magnets capable of withstanding extreme conditions.
- Automotive Industry: With the rise of electric and hybrid vehicles, the demand for NdFeB magnets capable of operating at high temperatures and resisting strong opposing magnetic fields is growing. GBD magnets, with their enhanced coercivity and reduced HREE content, are ideal for these applications, offering performance stability without the high cost of Dy and Tb.
- Renewable Energy: Wind turbines, particularly offshore installations, require large quantities of NdFeB magnets. GBD reduces the amount of HREEs needed, making these magnets more cost-effective and improving supply chain stability. The enhanced performance also allows for smaller, more powerful magnets, reducing the overall size and weight of wind turbine generators.
- Advanced Electronics: In mobile devices, energy-saving appliances, and other high-tech applications, GBD magnets provide the necessary magnetic strength and temperature stability without increasing production costs or compromising performance.
Limitations and Considerations
While GBD is a transformative technology, it is not without its limitations. The primary constraint of GBD is the penetration depth of the HREEs during diffusion, which typically reaches only about 5 mm per side. This makes the process less effective for thicker magnets, where uniform coercivity enhancement throughout the magnet may be required. Additionally, excessive diffusion times or temperatures can result in grain growth, which can negatively impact magnetic properties.
Grain boundary diffusion represents a significant leap forward in the production of NdFeB magnets. By concentrating HREEs at the grain boundaries, GBD enhances coercivity while maintaining high remanence, reducing the use of expensive and scarce materials like Dy and Tb. This process not only improves the performance and cost efficiency of magnets used in demanding applications but also allows for the creation of new magnet grades with properties that were previously unattainable. As the demand for high-performance magnets continues to rise across industries such as automotive, renewable energy, and advanced electronics, GBD stands as a critical innovation in magnet technology, ensuring a sustainable and efficient future for NdFeB magnets.
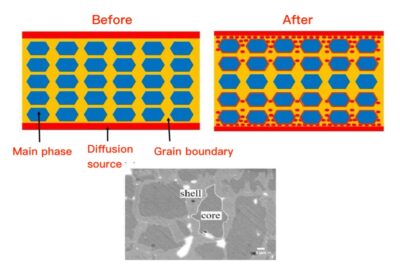
Grain Boundary Diffusion process
Leave A Comment